It’s January 2025, and many of the manufacturers I know are still neck-deep in strategic and operational planning. They need to get better at meeting customer commitments this year. They need to cut waste. They need to trim costs. They need to cut lead times to remain competitive. Most of all, they need to cut down on the day-to-day chaos that defines their world.
Sound familiar? No matter what business you are in, things happen fast in our hyper-competitive, 24X7X365 world. Chances are good that at least one of the goals I listed above applies to you and your organization.
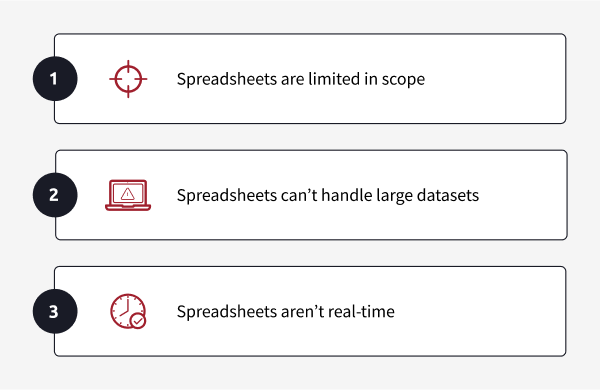
3 Reasons Your Spreadsheets Aren’t Working
Are you still managing production using spreadsheets? If so, you’re not alone. I see many manufacturers that rely on MRP for purchase and work orders and use spreadsheets for scheduling. Sometimes, these spreadsheets are sophisticated marvels of formulaic engineering. Other times, not so much. Either way, they all suffer from the same shortcomings:
#1 Spreadsheets are limited in scope.
Production-oriented spreadsheets are typically created to optimize resources individually without knowledge of how their localized decisions impact the flow of the overall value stream. For all but the simplest of facilities, it is impractical for production planners and managers to do the necessary calculations and work to optimize the entire business. When there are interdependencies between resources, and the number of resources in the production flow is greater than three or four, production planning via spreadsheets becomes virtually pointless. We will get into this more in my next post when I go deeper into the algorithms that power advanced planning and scheduling.
#2 Spreadsheets can’t handle large datasets.
If your manufacturing environment is complex, datasets can get large fast. Optimized planning and scheduling require taking into account material shortages, machine capacity, planned production, available labor, alternate resources, tooling, non-conformances, and other such variables. This level and volume of data along with the complexity of orchestrating a schedule from it is largely unfeasible for a spreadsheet. Even if the equations and potentially algorithms are successfully designed, the spreadsheet will be cumbersome and largely non-performant.
#3 Spreadsheets aren’t real-time.
By their nature, updating spreadsheets is typically a batch function. Given the speed at which complex manufacturers operate, data quickly can go stale, leaving the schedules generated from them behind and ineffective. If the production flow is at all complex, it can be difficult to keep up with the dynamic changes for even one resource or product line. Unless you can manage the variability, you cannot eliminate the chaos.
There are many areas of the business where spreadsheets are helpful, but they were not made to manage production in complex manufacturing environments, let alone address supply chain variability and ever-changing market demands facing today’s manufacturers. So, let’s turn to a tool that is: Advanced Planning and Scheduling, or APS.
What is Advanced Planning and Scheduling (APS) Software?
You’re probably already using some sort of software to manage your business, most likely an ERP system with a few operations modules installed, e.g., sales order processing, production, material requirements planning (MRP), and so on.
That’s a good start. ERP systems track which customers want what products and by when. If your ERP system includes MRP, it will tell you which materials need to be ordered. If your system is good, it may even provide insights into which jobs need to be prioritized and when your materials need to arrive in order to meet the promised timelines. (But realistically, we’re already getting into spreadsheet territory for a lot of ERP users.)
Advanced Planning and Scheduling (APS) software takes over where ERP/MRP systems leave off by synchronizing the operational elements of your business to make sure that the right materials are where they need to be at the right time to make the right products. APS is also designed to ensure everyone on the operational side of the business is working on the right jobs.
If you’re thinking of implementing continuous improvement strategies over the course of the year, e.g., lean, six sigma, theory of constraints (TOC), etc., APS can help with that too. Without APS, these methods often fail as manual implementation of these approaches to production management just can’t keep up.
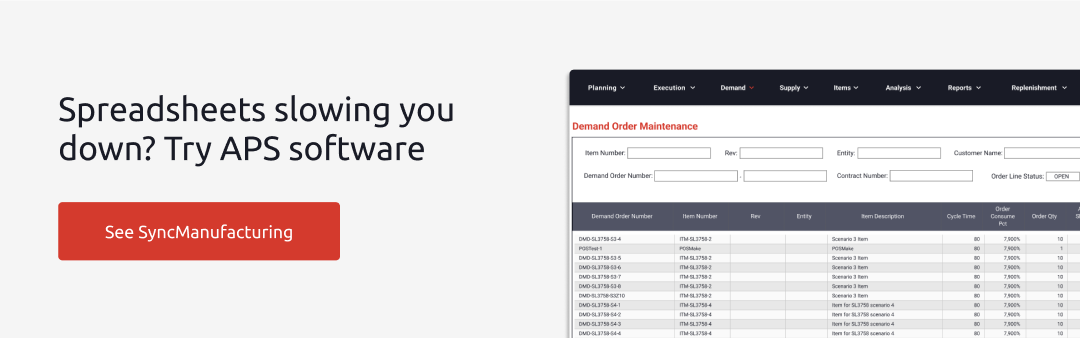
Gain Clarity, Control, and Confidence
By moving beyond spreadsheets and leveraging advanced technologies like APS, manufacturers can not only deliver industry-leading levels of customer satisfaction, but they can also promote a range of internal benefits, including less waste, lower costs, and an improved working environment.
Of course, you’ll want to look for an APS application that integrates easily with your existing ERP system. Once implemented, your APS system will become the defacto hub of your operations, helping to keep everyone on the same page and every element of the business synchronized on meeting your customer commitments.
With SyncManufacturing® from Synchrono®, you gain the clarity, control, and confidence needed to thrive in today’s fast-paced manufacturing landscape. Our solution can transform your approach to production planning and scheduling, with the visibility and insights needed to streamline operations and fill gaps that spreadsheets can’t. To learn more, contact us or request a private demo.
Next Up: The Role of Algorithms in APS
Advanced algorithms are the engine that drives APS applications, so in my next post, we’ll dig deeper into how they work. In the meantime, if you have questions, feel free to reach out to me. Until then, may this year be productive and profitable for everyone!