Become Demand-Driven for Efficiency and Growth
In today’s unpredictable market, manufacturers face constant challenges—overstocking, wasted resources, and missed opportunities due to shifting customer demands. The solution? Transitioning to a demand-driven model. By producing only what’s needed, when it’s needed, based on real-time demand signals.
Demand-Driven Manufacturing enables a synchronized, closed loop between customer orders, production scheduling, and manufacturing execution – all while synchronizing the flow of materials and resources across the supply chain. They key components are synchronization and flow. Demand-driven Manufacturing is associated with “Response Planning” or “Pull” manufacturing and supply chain methods. The two main continuous improvement approaches that advocate the demand/pull method are Lean Manufacturing and Constraints Management. You can see elements of these methodologies throughout Synchrono systems and our Synchrono Demand-Driven Manufacturing Platform.
Environments for Demand-Driven Manufacturing
Demand-driven principles can be used in nearly every manufacturing environment because the focus is on flow through the factory. In make-to-stock (MTS) environments, a Demand-Driven Manufacturing platform can drive immediate improvements by right-sizing inventory, increasing flow and throughput, and replenishing resources using a kanban system. These improvement can be extended across the entire supply chain. In a make-to-order (MTO), engineer-to-order (ETO), and configure-to-order (CTO) environments, a demand-driven manufacturing planning, scheduling and execution approach delivers increased flow, throughput, on-time delivery and clarity throughout the manufacturing process and the extended supply chain.
In any environment, a Demand-Driven system will synchronize process, people, machine, materials, method and information. During execution, work released to the shop floor is in full alignment with the capacity of the constraint, minimizing work-in-process (WIP), and driving flow. Order statuses (and any associated disruptions) are visible throughout the enterprise – to the production team, supply chain management, customer service, sales and leadership. Everyone is working form the same factual, real-time information.
Synchrono® developed CONLOAD™, a patented method for gating work into the system based on the capacity of constraints. CONLOAD™ is a component of SyncManufacturing® software for demand-driven manufacturing planning, scheduling and execution. If you would like to see how CONLOAD™ works, this video provides a good overview:
Demand-Driven Business Value
Evidence from existing Demand-Driven Manufacturing environments supports the evolution to this method. Some of the results that synchronized, technology enabled, Demand-Driven Manufacturers have experienced include:
Lower Operating Expenses
Many Demand-Driven Manufacturers gain greater visibility, allowing them to curtail waste, lower WIP and align around flow—creating more business value in the form of profitability and reduced expenses.
Greater Inventory Control
Customer orders mandate inventory consumption—advanced demand-driven software systems spark only what is needed to meet demand.
Workforce and Processes Aligned Around Flow
When manufacturing planning, scheduling and execution are synchronized with demand, everyone is aligned to address constraints, enhance flow and increase capacity
Increased Throughput
Based on better control of flow, visibility and constraints management, more throughput is generated, which is directly tied to profitability.
Effective Use of Resources Creates Profitable Growth Opportunities
Eliminate waste and free up capacity to grow product lines or expand into new markets without added overhead.
Real-Time Metrics
Signals from every step in the process are integrated by connected systems, providing solid direction for continuous improvement initiatives and metrics that reflect a “single version of the truth.”
Customer Orders Drive Action
Everything is triggered by customer orders, so consumption becomes more effective.
Competitive Advantage
Customers get what they want when they want it and you become the preferred vendor.
Cost Savings
Investing in synchronized production systems can streamline operations and eliminate expenses tied to business growth challenges.
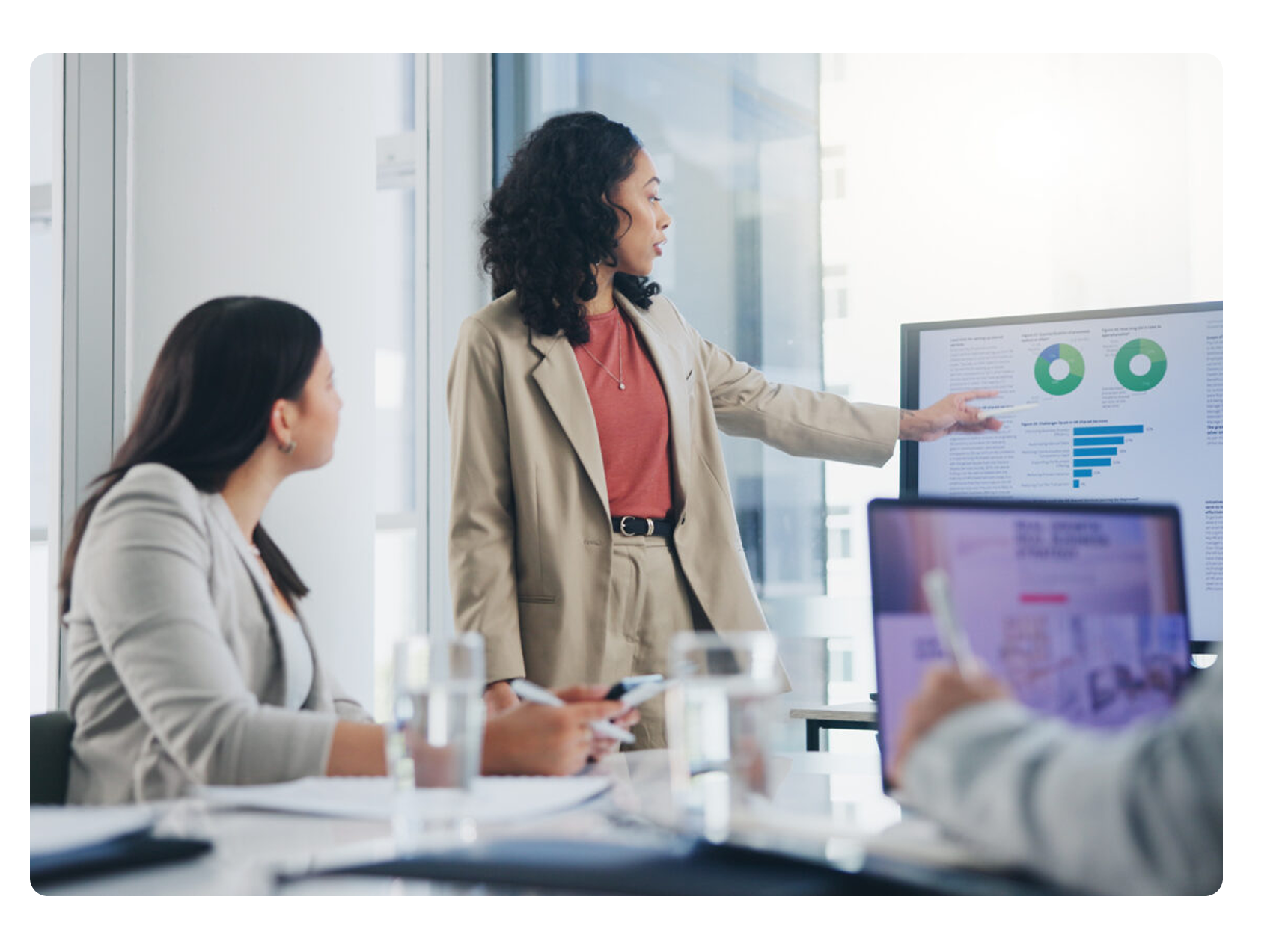
Demand-Driven KPIs
The Key Performance Indicators (KPIs) monitored in a Demand-Driven Manufacturing environment track the demand signal through the entire organization. The results measured are those related to flow, velocity, throughput, and other measures of movement throughout the supply chain. These KPIs are often used to guide the organization to areas of focus for continuous improvement. Finally, the true key performance indicator for Demand-Driven Manufacturers is on-time delivery.
Flow-Based Metrics
High-performing delivery KPIs and metrics – coupled with customer satisfaction – open up additional business opportunities based on expanded capacity and enhanced resource utilization.
Start Your Demand-Driven Journey Today
In using demand-driven principles and synchronized systems, manufacturers have learned to reach new levels of communication, growth and customer responsiveness. Every forward-thinking manufacturing environment is somewhere on the path toward becoming more synchronized and demand-driven. Where are you?