Lean Manufacturing relies heavily on trusted relationships with suppliers and pre-negotiated terms of engagement. Through the use of supplier quality certifications and blanket (long-term) purchase orders, a manufacturer can accurately and effectively calculate the optimal level of inventory needed to fulfill demand requirements through the duration of replenishment lead time.
Ensuring supplier performance
When a relationship is setup with a supplier, a service level agreement is defined. Items such as negotiated lead times, packaged quantities, order receipt confirmations, and advanced shipment notices must all be specifically spelled out. An eKanban Pull-based inventory replenishment system monitors that each aspect of the service level agreement is being met by the supplier in real-time. If they are not, a series of alerts and notifications are issued to all interested and affected parties. This gives everyone a chance to quickly adjust their behavior to bring performance back in line.
eKanban software also makes all of this real-time information available for historical analysis and to identify trends in performance. Late shipments, short shipments, and other supply chain performance concerns are all captured and presented in terms of percentage of conformance to the service level agreement. These reports give everyone in the supply chain information about how to focus their continuous improvement energies.
Eliminating inventory waste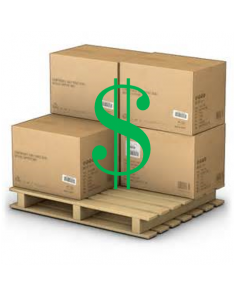
eKanban is heavily based on Lean and Six Sigma principles and tools, and adds focus to these efforts by eliminating inventory waste through real-time demand signaling and just-in-time replenishment.
eKanban replenishment is based on the notion that if you take one, you make one. As such, you are reducing on hand inventory and not building assemblies or products without actual demand. You dramatically reduce the amount of inventory that becomes old or obsolete, free warehouse space and you build flexibility – and potential capacity – into your production process. An eKanban system exposes this flexibility so that manufacturers and suppliers can rapidly evaluate the true capability of the system to respond to a specific change in demand.
Manufacturing operations utilizing Lean are increasingly implementing Pull systems with more suppliers. And eKanban systems are taking hold as a relatively easy, and non-disruptive way to introduce Lean thinking into the organization – and bank on a quick return. Just in “right-sizing” inventory levels alone, some manufacturers have saved millions and added tens of millions back to cash flow that can be put to use in more productive ways than filling a warehouse. Additional savings are being realized in improved supplier relationships, lead times and inventory turns – and a dramatic reduction in administrative paperwork.
If you have an experience using a manual or eKanban system, please add a comment. I’d like to hear it!
Additional Resources:
Case Study: Dynisco, A Roper Company
White Paper: Exploring Push v. Pull Manufacturing with Kanban