Resources
Our collection of resources covers industry issues related to Demand-Driven Manufacturing, Lean Manufacturing, the Internet of Things and more. And evaluate Synchrono® software through our case studies, videos and focused product information.
Receive new resource information from Synchrono® as it becomes available by syncing up with us. And tune into the Demand-Driven Matters blog for a variety of perspectives on issues related to Demand-Driven Manufacturing, Lean Manufacturing, Theory of Constraints, and more.
Search through our resources by type, topic or product.
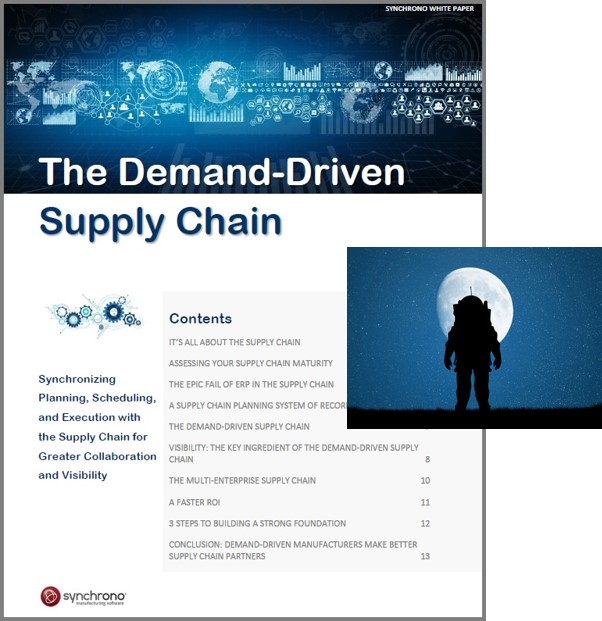
White Paper: The Demand-Driven Supply Chain
As manufacturing technology evolves, more options become available for managing the increasing complexity of today’s supply chains. This paper provides guidance for evaluating your supply chain processes and how you compare to others on the technology spectrum. Learn why and how more demand-driven manufacturers are establishing a supply chain planning system of record to synchronize activities throughout their supply chain to improve production flow. Real-world examples are provided on how manufacturers are applying technologies to better optimize and visualize their supply chains.
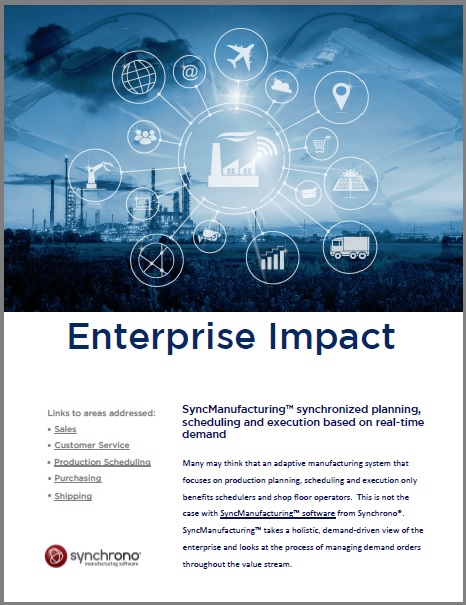
White Paper: Enterprise Impact of SyncManufacturing® Software
When demand signals are received by a manufacturer, the manufacturer needs systemic synchronization of all key resources to ensure a company-wide focus on achieving the highest level of customer satisfaction and delivery:
- Labor, materials and operational capabilities are available to execute the presented demand;
- Execution signals are properly aligned throughout the manufacturing process;
- All resources are focused on the right demand priorities and do not waste capacity (machine, labor, materials) or create chaos during the production process.
The benefits of synchronization extend beyond schedulers and shop floor operators. Enterprise Impact addresses how ROI is extended across the organization to sales, customer service, production scheduling, purchasing and shipping.
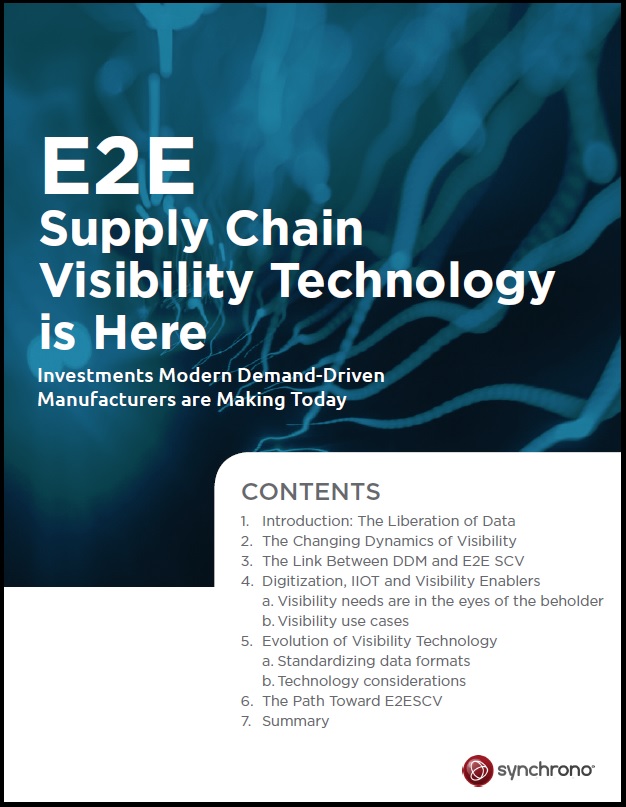
White Paper: End-to-End Supply Chain Visibility Technology is Here
Visibility continues to be a top concern for supply chain leaders across the globe. End-to-End Supply Chain Visibility Technology is Here, addresses new technologies for enabling end-to-end supply chain visibility – and its link to modern Demand-Driven Manufacturing. Through research and case studies, the paper offers guidance in building a business case for end-to-end supply chain visibility technology by covering how, why, and where Demand-Driven Manufacturers are investing today.
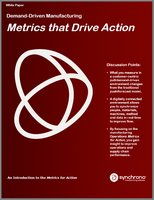
White Paper: Demand-Driven Manufacturing Metrics that Drive Action
Demand-Driven Manufacturing Metrics that Drive Action addresses the key elements of demand, or pull-based manufacturing: Managing constraints and synchronizing activities to improve production flow and, ultimately, throughput. In doing so, this white paper lays the foundation for the Demand-Driven Manufacturing Metrics for Action Guide – a resource that outlines the operational metrics that you can take action on to improve your operations and supply chain performance.
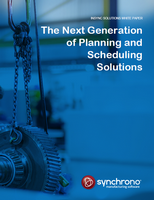
White Paper: The Next Generation of Planning and Scheduling Solutions
This paper provides a customer/order-centric view of manufacturing planning and scheduling that focuses on synchronizing man, material, method and machine to produce an order in the most efficient way possible. This approach drives the system – and those who use it – to optimize flow through the entire system rather than individual components. Focusing on flow through the entire process leads to increased throughput and ultimately impacts the bottom-line.
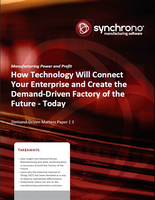
White Paper: How Technology Will Connect Your Enterprise and Create the Demand-Driven Factory of the Future – Today
The Industrial Internet of Things (IIoT), Smart Manufacturing, Industry 4.0 and the Factory of the Future all point toward a digitally connected environment where manufacturing is based on actual customer demand. How Technology Will Connect Your Enterprise and Create the Demand-Driven Factory of the Future – Today reviews these strategies – along with how and why manufacturers are enabling them today.
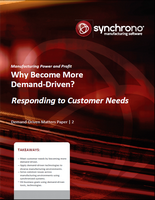
White Paper: Why Become More Demand-Driven? Responding to Customer Needs
When the focus of every business is on revenue growth and meeting specific customer requirements, the need to become demand-driven speaks for itself. This paper will help you outline your business case more efficiently with evidence from similar manufacturing environments that successfully transitioned.
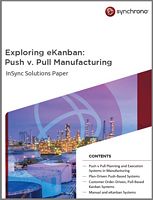
Exploring eKanban: Push v. Pull Manufacturing
If you’re considering a shift from a traditional, push-based MRP manufacturing system to a more progressive pull-based system, this white paper is a must read. While contrasting both types of systems, the paper explores the nature of pull-based manufacturing and the evolution of Kanban systems to support today’s demand-driven manufacturing environment.
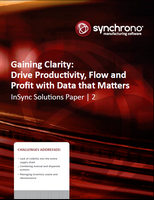
Kanban Series White Paper: Gaining Clarity: Drive Productivity, Flow and Profit with Data that Matters
Many of today’s discrete manufacturers are overcoming the challenges of legacy push-based systems by turning to pull-based eKanban software systems that focus on throughput and flow and result in a reduction in costs and inventory. This resource explores manufacturing Kanban systems from a management perspective, detailing the benefits of a more predictable environment with the decision-making power gained through deeper access to real time data and analytics.
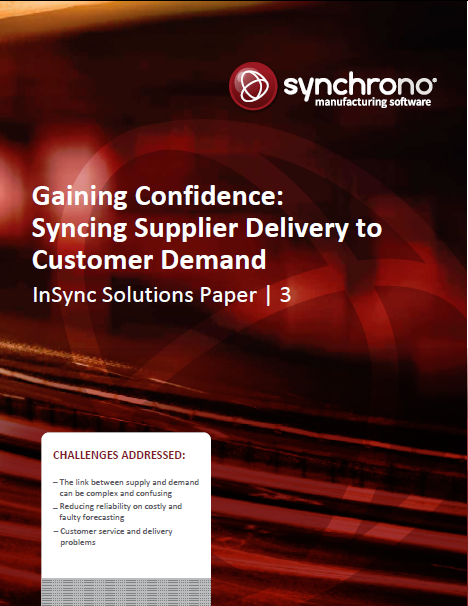
Kanban Series White Paper: Gaining Confidence: Syncing Supplier Delivery to Customer Demand
Demand-driven and lean production allows manufacturers to be more responsive to consumer needs while increasing their own profitability. It also reduces the reliance on forecasts by linking demand signals and providing real-time data directly to suppliers. Customers, in turn, demonstrate their confidence by eliminating buffers. This works to build lasting client relationships by ensuring customer service that exceeds expectations and drives results. Download this resource to learn more.
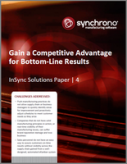
Kanban Series White Paper: Gain a Competitive Advantage for Bottom-Line Results
In this white paper, we look at the competitive edge Demand-Driven Manufacturers gain by not only being devoted to driving flow and eliminating waste, but also in enabling their organizations to become best-in-class by using Pull and eKanban software technology. These manufacturers provide valuable opportunities to their customers and, because of their Lean Manufacturing approach and continuous improvement efforts, are equipped to increase their effectiveness, productivity and capacity while achieving a competitive advantage in the marketplace.
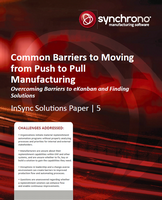
Kanban Series White Paper: Common Barriers to Moving from Push to Pull Manufacturing
This resource addresses the following challenges:
- Organizations initiate material replenishment automation programs without properly analyzing processes and priorities for internal and external stakeholders.
- Manufacturers are unsure about their current replenishment capabilities within ERP and other systems, and are unsure whether to fix, buy or build a solution to gain the capabilities they need.
- Disruptions in leadership and a change-averse environment can create barriers to improved production flow and automating processes.
- Unanswered questions regarding whether a replenishment solution can enhance flow and enable continuous improvements.
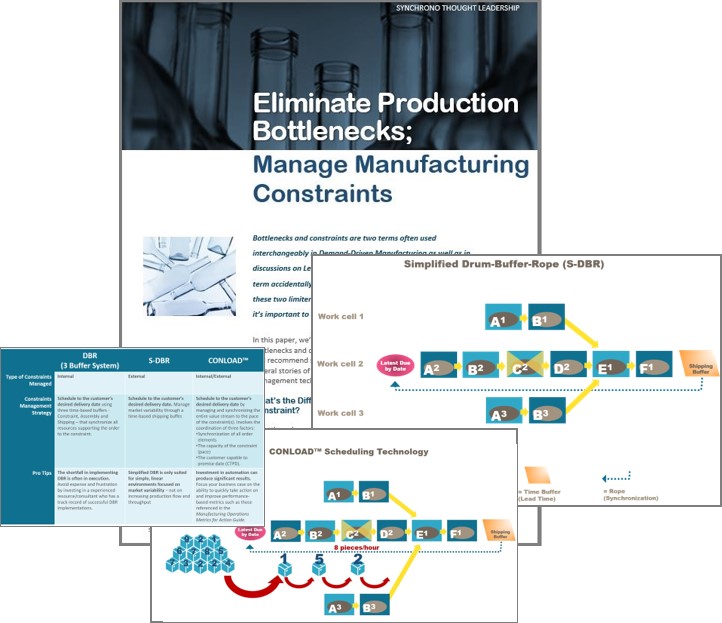
Thought Leadership: Eliminate Production Bottlenecks; Manage Manufacturing Constraints
What is the difference between a bottleneck and a constraint? And, what’s the best strategy for managing each of these inhibitors to production flow?
Eliminate Production Bottlenecks; Manage Manufacturing Constraints explains how Lean and Demand-Driven Manufacturers categorize constraints and bottlenecks – and why they need to be addressed differently. The paper reviews:
- Different strategies for managing bottlenecks and constraints while accounting for variability.
- How production flow-based constraints have been addressed through different Drum-Buffer-Rope (DBR) methods from The Theory of Constraints (TOC)
- How DBR concepts have evolved into technology that synchronizes the entire value stream and automatically sets the optimal production pace to drive flow.
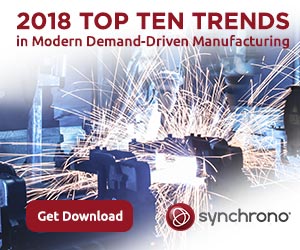
Thought Leadership: 2018 Top Ten Trends in Modern Demand-Driven Manufacturing
With all signals pointing toward a good year, manufacturers have a decision to make. They can enjoy the strong economy while it lasts or look to the future and invest in technologies that will help them build a stronger organization that can prosper through economic shifts.
Last year, the common thread throughout our Top Ten Trends in Modern Demand-Driven Manufacturing list was digitization, synchronization and visualization. This year’s trends revolve around the maturity – and execution – of these concepts.
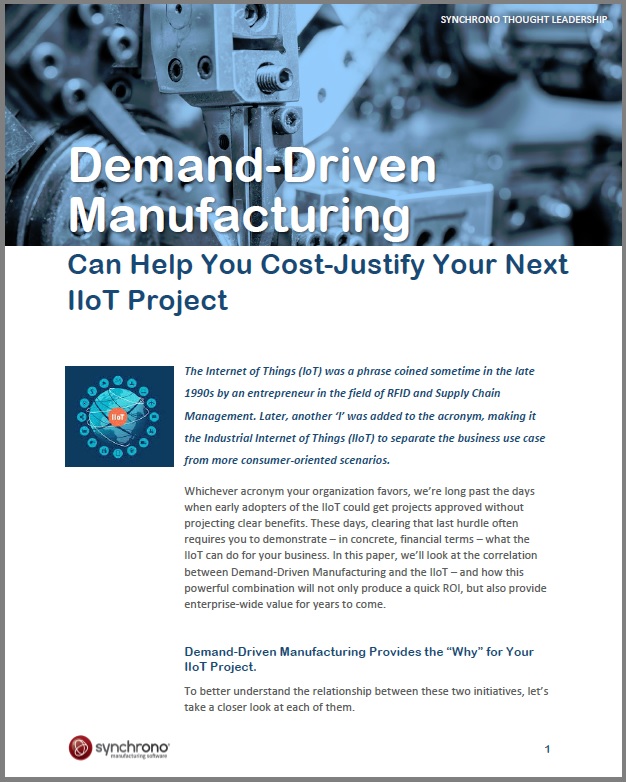
Thought Leadership: Demand-Driven Manufacturing Can Help You Cost-Justify Your Next IIoT Project
While the Industrial Internet of Things (IIoT) connects data assets, manufacturers need to think about how they are going to curate this data and transform it into actionable – and quantifiable – results. This paper offers the method of Demand-Driven Manufacturing as the link to IIoT value creation across the organization. Cost-justification examples touch on preventative maintenance, just-in-time material replenishment, quality assurance and increased throughput created by synchronizing planning, scheduling and production execution data.
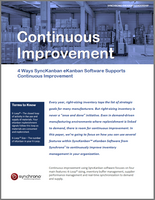
Thought Leadership: 4 Ways SyncKanban® eKanban Technology Drives Continuous Improvement
Every year, right-sizing inventory tops the list of strategic goals for many manufacturers. But right-sizing inventory is never a “once and done” initiative. Even in demand-driven manufacturing environments where replenishment is linked to demand, there is room for continuous improvement. This paper focuses on how you can use several features within SyncKanban® eKanban Software to continuously improve inventory management in your organization.
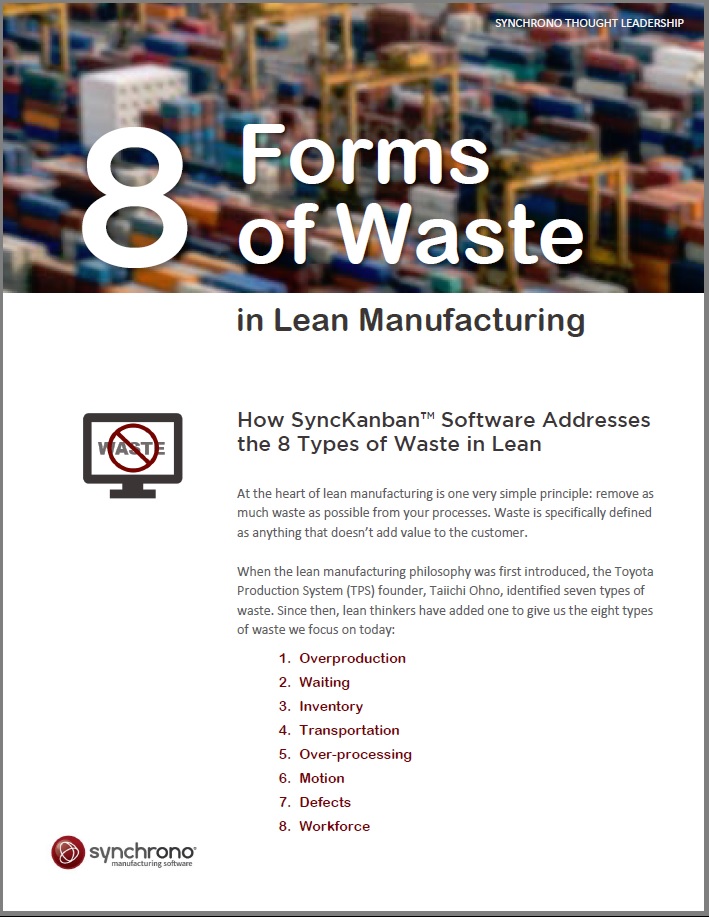
Thought Leadership: 8 Forms of Waste in Lean Manufacturing
At the heart of lean manufacturing is one very simple principle: remove as much waste as possible from your processes.
Lean practitioners have identified 8 forms of waste that occur in manufacturing. And while there are many ways to eliminate these 8 forms of waste, when comparing the level of effort to potential return, implementing eKanban is one of the most attractive lean initiatives there is. Download 8 Forms of Waste to learn how SyncKanban® eKanban software addresses each form of waste.
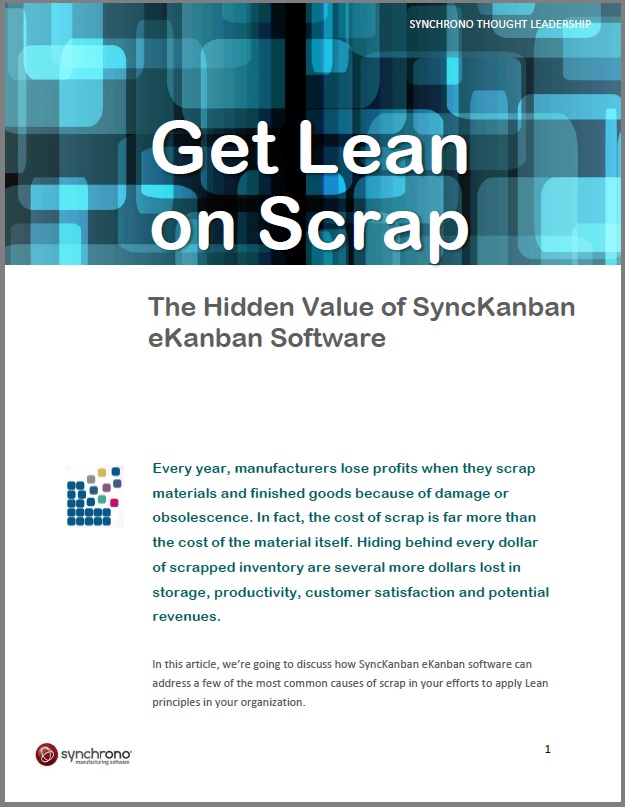
Thought Leadership: Get Lean on Scrap
Every year, manufacturers lose profits when they scrap materials and finished goods because of damage or obsolescence. In fact, the cost of scrap is far more than the cost of the material itself. Hiding behind every dollar of scrapped inventory are several more dollars lost in storage, productivity, customer satisfaction and potential revenues.
This paper reviews one of the hidden benefits of eKanban software: Scrap reduction. Download Get Lean on Scrap to learn how SyncKanban® software can help address the most common causes of scrap and accelerate your efforts in applying Lean principles in your organization. You’ll learn:
- How to use Manufacturing, Supplier and Tugger Route eKanbans to reduce defective, damaged and obsolete inventory
- Why you should pay attention to a new metric: Queue Turns
- How one manufacturer reduced 90% of their scrap in just three months
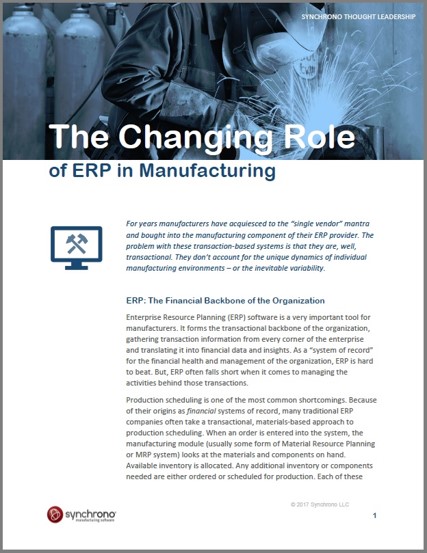
Thought Leadership: The Changing Role of ERP in Manufacturing
ERP is a great system of record for managing transactions – and the financial health and management of the organization – but often falls short when managing the activities behind those transactions. Production scheduling is one of the most common shortcomings. This paper reviews the evolution of production planning, scheduling and execution “tools” and why more manufacturers are abandoning spreadsheets, MRP and other software – and turning towards a planning system of record that sits on top of their ERP to manage manufacturing operations and the extended supply chain.
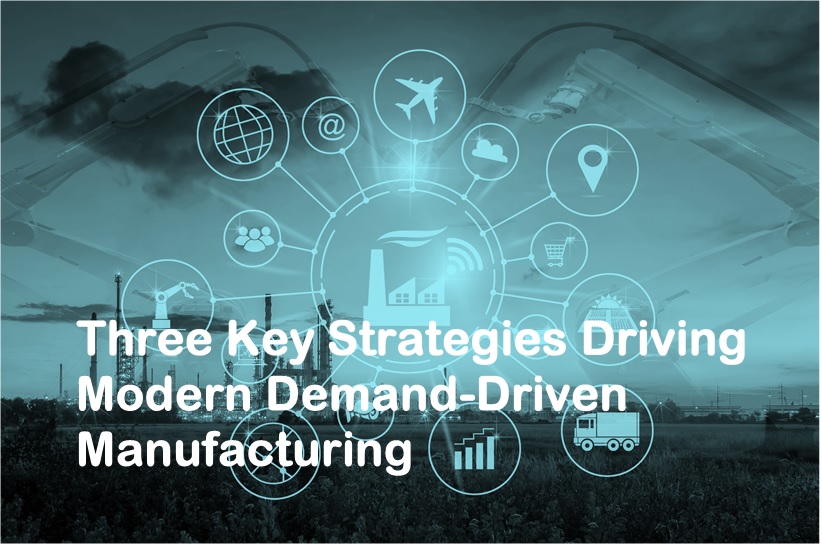
Thought Leadership: Three Key Strategies of Modern Demand-Driven Manufacturing
Today’s manufacturers are meeting complex market demands while maintaining desired levels of customer satisfaction, supplier performance and production throughput by applying Modern Demand-Driven Manufacturing strategies that enable a more connected environment and serve as the catalyst for progressive concepts, including:
- The Industrial Internet of Things
- Smart Manufacturing
- Synchronized Planning, Scheduling and Execution
- End-to-end Supply Chain Visibility
Download this paper for an overview of the three key strategies of Modern Demand-Driven Manufacturing.
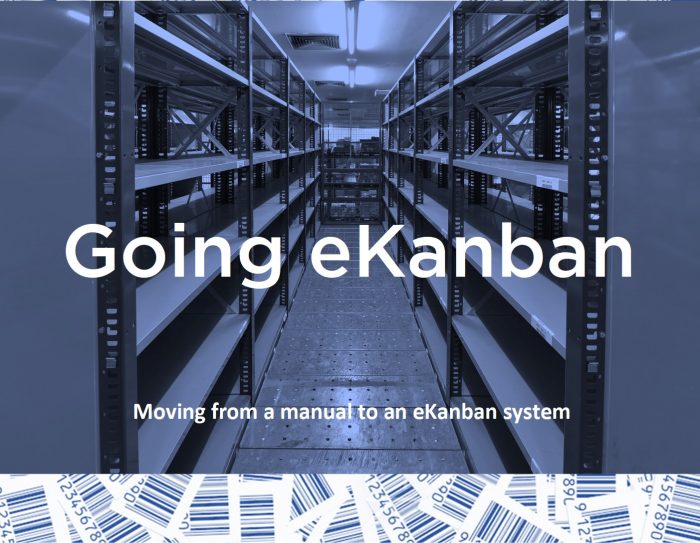
Thought Leadership: Going eKanban
This article provides insight for manufacturers currently using a manual Kanban process (physical cards) or homegrown Kanban software for replenishment that they have outgrown. This paper will answer:
- When is the right time to move to an automated eKanban software system?
- Steps for a successful eKanban rollout.
- Typical eKanban results
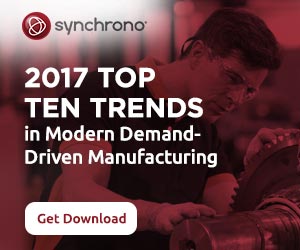
Report: 2017 Top Ten Trends in Modern Demand-Driven Manufacturing
The 2017 Top Ten Trends for Modern Demand-Driven Manufacturing is based on interactions with hundreds of manufacturers and industry experts – addressing challenges, supporting innovation and introducing technologies. The constant, key themes that rise to the top are digitization, synchronization and visibility.
The 2017 Top Ten Trends report provides descriptions and real-world examples of each trend. Download the report here:
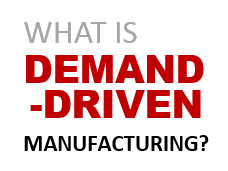
Thought Leadership: What is Demand-Driven Manufacturing?
Demand-Driven Manufacturing combines the best of Lean Manufacturing, Theory of Constraints and Six Sigma principles. Find out why more and more manufacturers are turning to the proven methods of Demand-Driven Manufacturing to synchronize their operations, improve flow and gain a competitive edge. Download this resource brief on Demand-Driven Manufacturing to learn more.
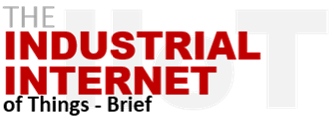
Thought Leadership: The Industrial Internet of Things (IIoT)
Imagine a fully connected manufacturing environment where data from machines, tools, applications and software systems merge to intelligently deliver instant insight helping you to drive performance metrics, innovation, OEE, quality, continuous improvement initiatives and more. This resource explores how a connected environment can have transformational value and solutions that can help you enable the IIoT today.
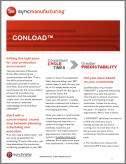
Thought Leadership: CONLOAD™ Scheduling Methodology
The two key elements of Demand-Driven Manufacturing are synchronization and flow. That is, the ability to synchronize production activities in order to drive flow. And while Synchrono® synchronizes (as the name implies) all layers of manufacturing operations and the extended supply chain, this article addresses the company’s patented scheduling methodology for driving flow: CONLOAD™.
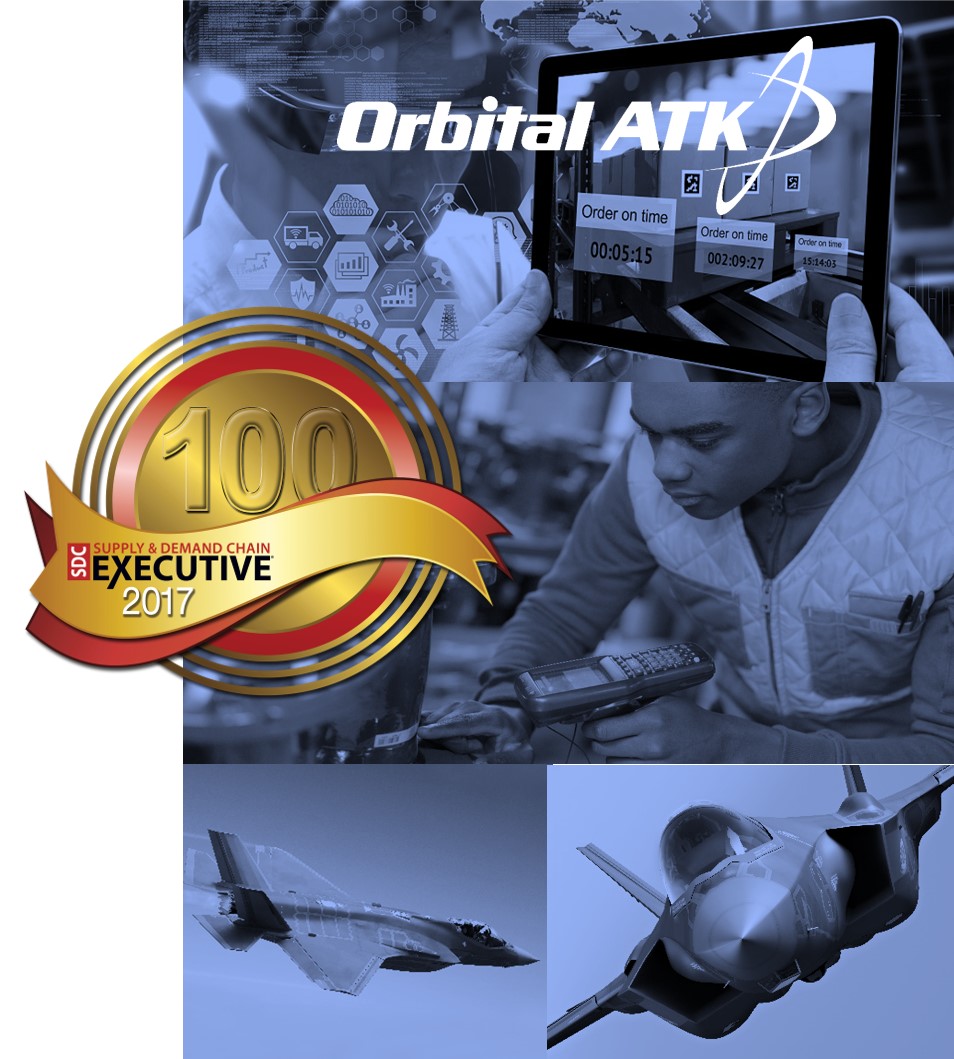
Customer Case Study: Orbital ATK Proves the Merits of SyncKanban®
This case study reviews the strategy and results of a new Lean project at the Aerospace Structures Division (ASD) of Orbital ATK. The goal of the project was to impact two key inventory metrics – improve inventory turns and reduce inventory cost; specifically, waste associated with material scrap.
- 30% WIP Inventory Reduction
- 90% Reduction in Scrap
- Consolidated 16 Replenishment Processes into SyncKanban®
Download the case study to learn why this project was awarded one of the top 100 supply chain projects by Supply & Demand Chain Executive.
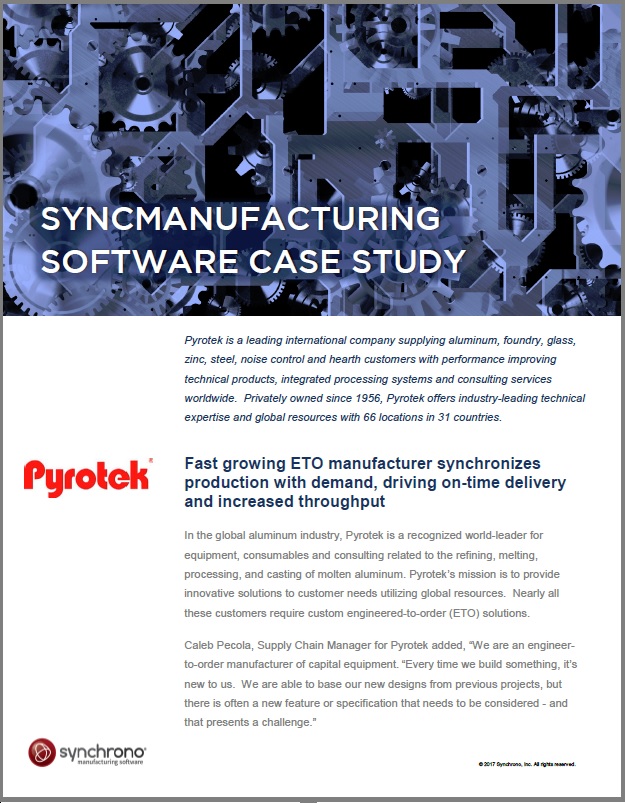
Customer Case Study: Pyrotek
After acquiring more complex equipment and expanding its product line, Pyrotek – a global engineering leader and innovator of performance-improving technical solutions and services for the aluminum industry – experienced tremendous growth. Growth that was compounded by the fact that as an engineer-to-order (ETO) manufacturer of capital equipment, every project they build is unique.
Read the case study to learn how SyncManufacturing® software helped them to be more compliant and disciplined. As a result, they are operating better as an organization.
Video Case Study: How Orbital ATK is Leveraging the IIoT and Visual Factory Technology to Drive Continuous Improvements.
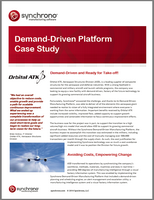
Customer Case Study: Orbital ATK
Orbital ATK, Aerospace Structures Division (ASD), is a leading supplier of composite structures for the aerospace and defense industries. With a strong foothold in commercial and military aircraft and launch vehicle programs, the company was looking to equip a new facility with demand-driven, factory of the future technology to support its growing commercial aircraft business.
Read the case study to learn how the Synchrono® Demand-Driven Manufacturing Platform helped Orbital ATK create an award-winning transformation.
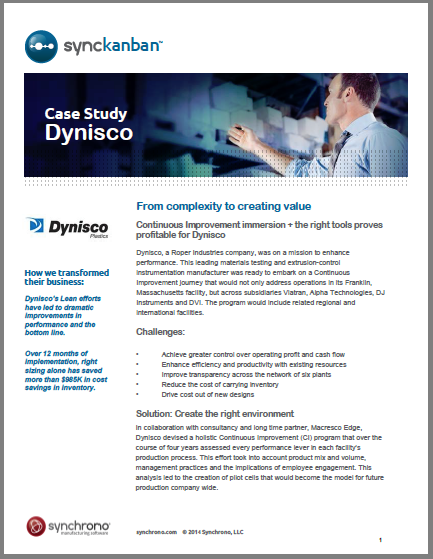
Customer Case Study: Dynisco
Today’s manufacturing eKanban software systems are not only equipped to manage highly complex environments, but provide a wealth of hidden benefits. Benefits that Dynisco, a leading materials testing and extrusion-control instrumentation manufacturer, realized after implementing SyncKanban® software, an electronic manufacturing Kanban solution from Synchrono®.
In upgrading from a manual to a manufacturing eKanban software system, Dynisco addressed 5 key business challenges and achieved significant reductions in inventory costs, lead times and more. What’s more, their 66-step manual manufacturing Kanban process to report inventory and supplier data was reduced to just 6 easy steps.

Customer Case Study: Wenger Manufacturing
Wenger Manufacturing, an engineer-to-order manufacturer, headquartered in Sabetha, Kansas, specializes in state-of-the-art commercial extrusion systems including industrial dryers, toasting ovens and mixers for the cooking industry.
Read the case study to learn how Synchrono® software helped Wenger Manufacturing reduce cycle time, manage capacity and more.
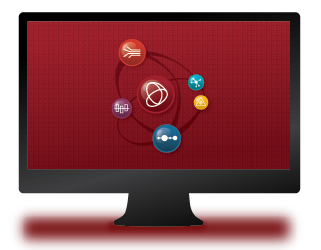
Video: Synchrono® Demand-Driven Manufacturing Software Platform
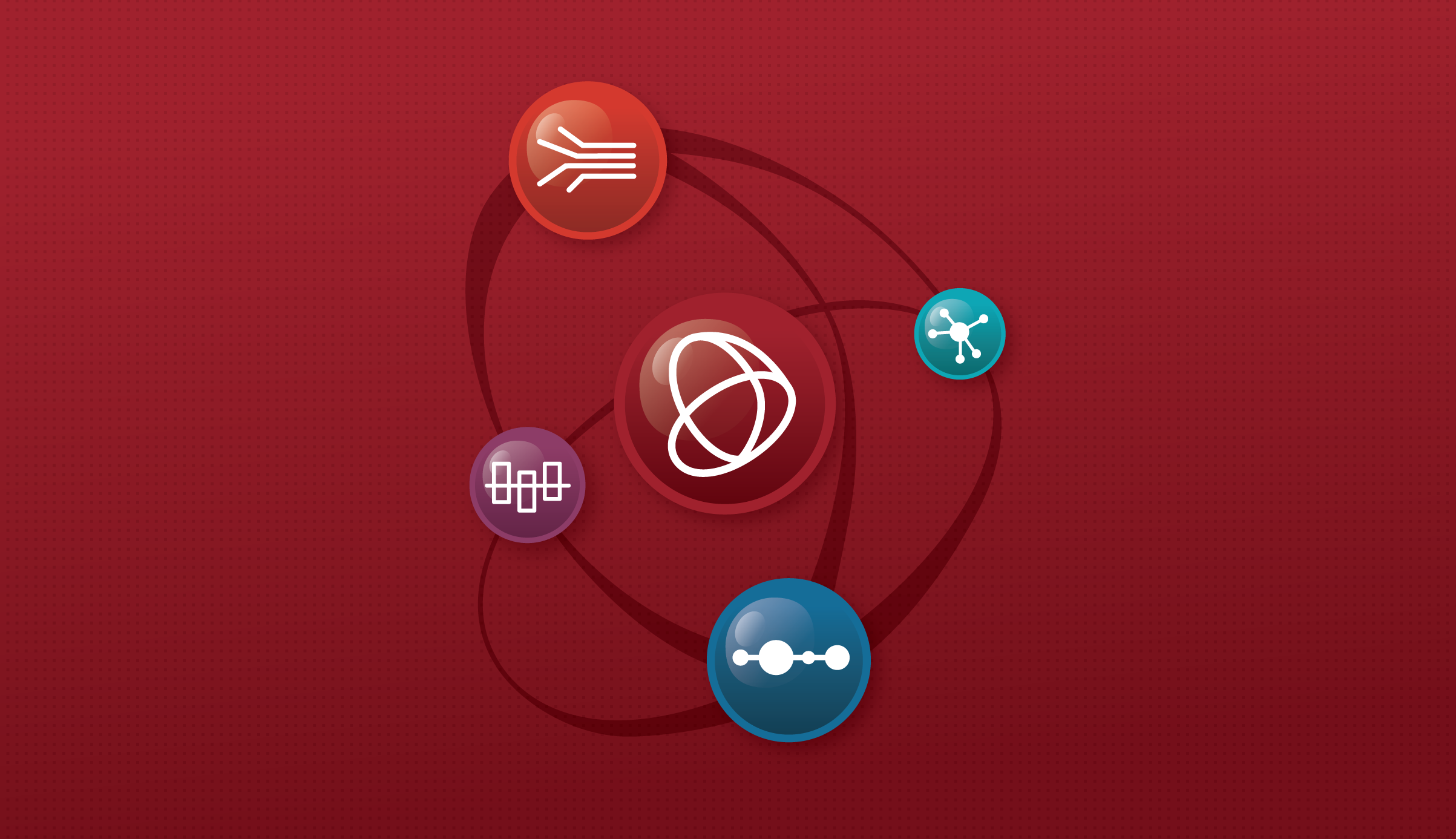
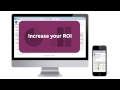
Video: SyncKanban® Manufacturing eKanban Software
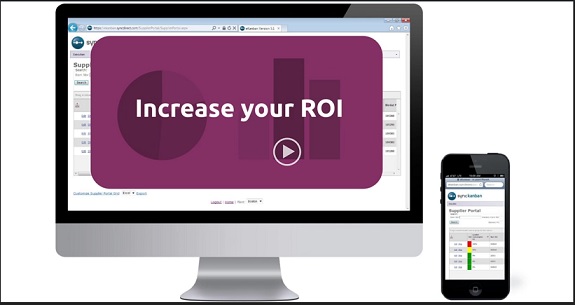
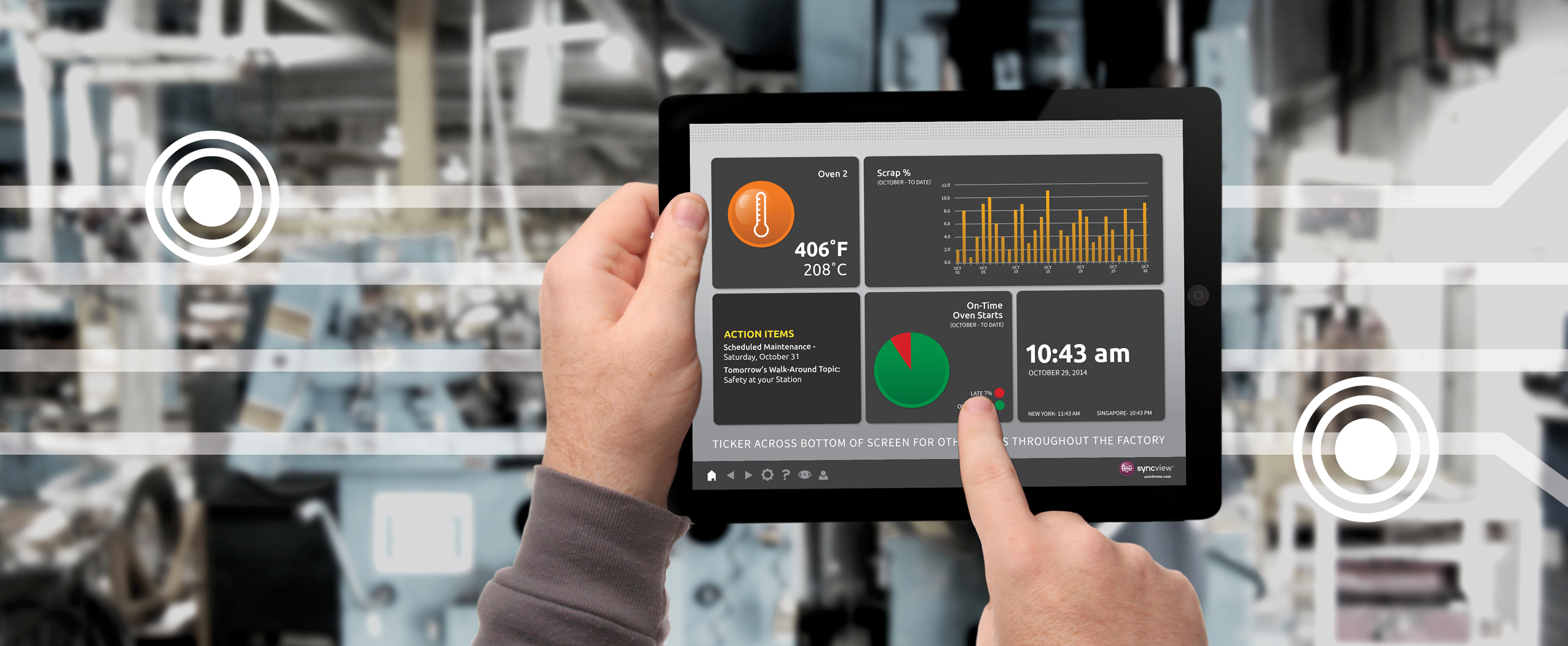
Video: SyncView® Real-Time Manufacturing Visualization System – 4 min. Overview
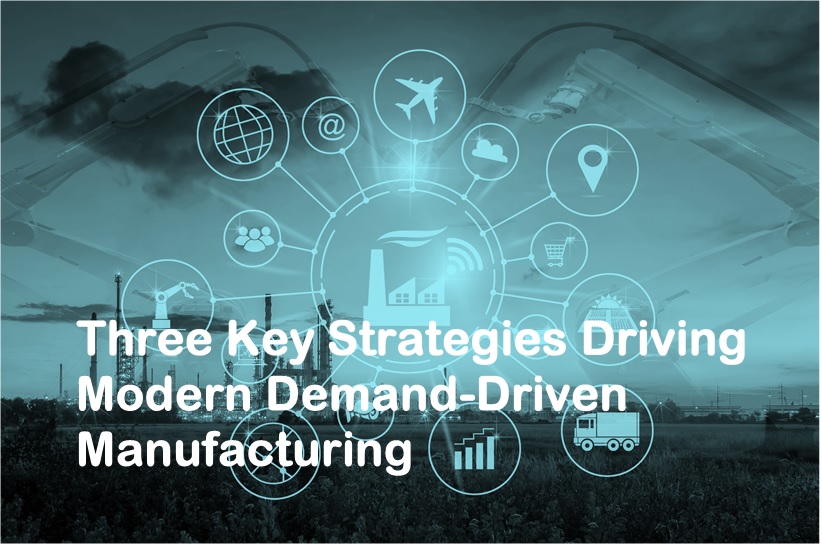
Video: The 3 Key Strategies Driving Modern Demand-Driven Manufacturing
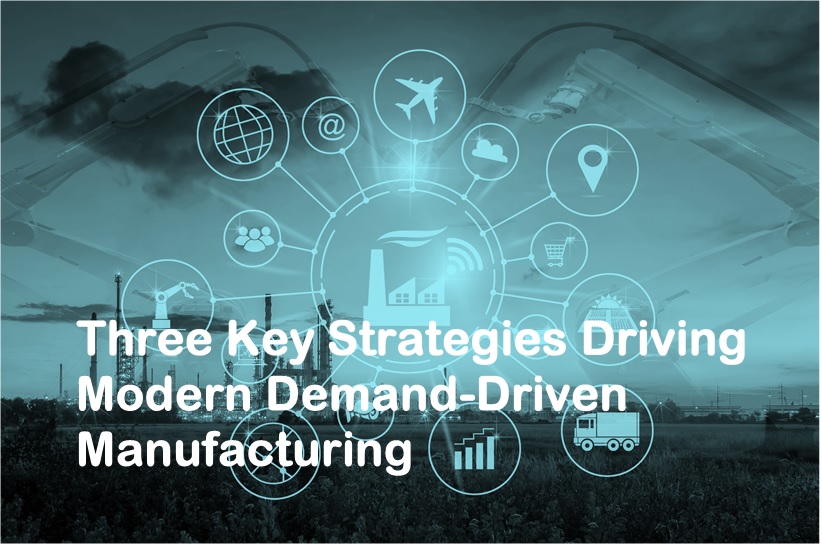
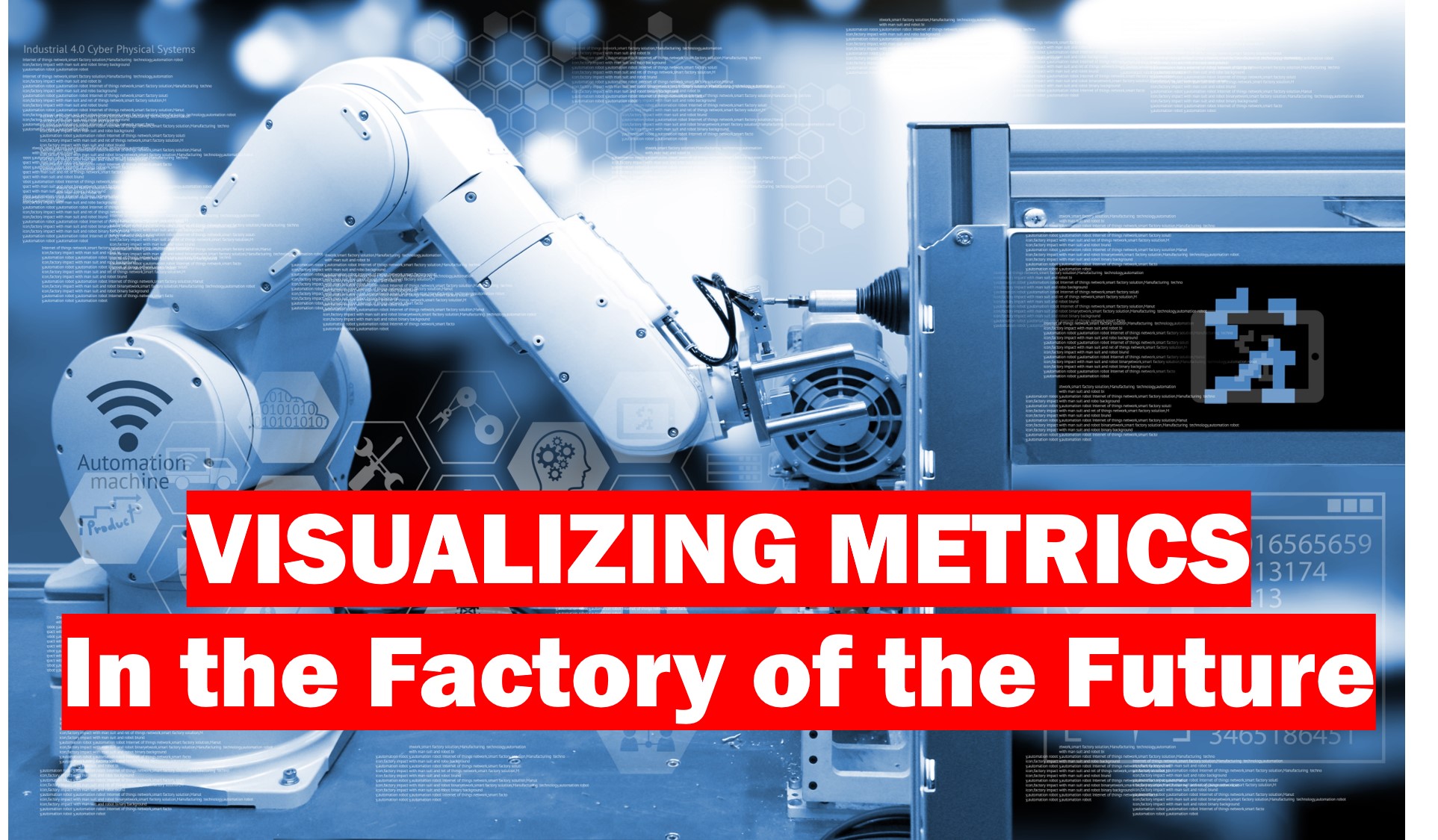
Video: Visualizing Metrics in the Factory of the Future
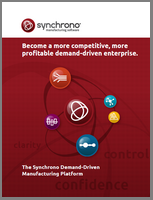
Brochure: Synchrono® Demand-Driven Manufacturing Platform
The Synchrono® Demand-Driven Manufacturing Platform is a collection of systems that enables the real-time visual factory of the future. We’ve combined the power of demand-driven manufacturing planning and scheduling with operations capabilities and more to provide everyone at every level of your organization with a dynamic view of what’s happening at every stage of your manufacturing process; from order inception through production and delivery.
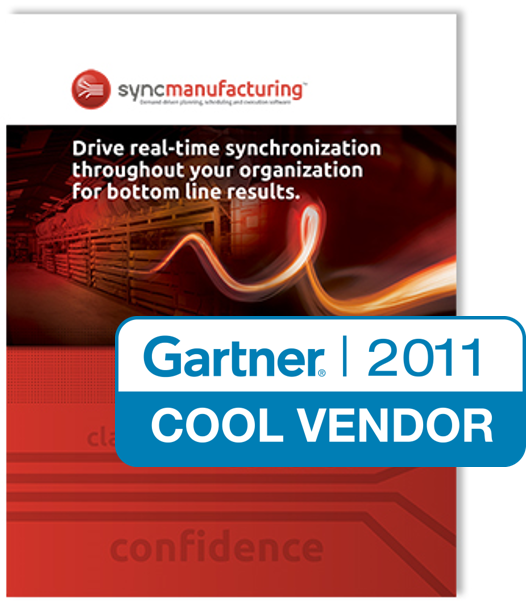
Brochure: SyncManufacturing® Software
Demand-Driven Planning, Scheduling and Execution Software
SyncManufacturing® planning and scheduling software simplifies production scheduling, eliminating the need to build and update schedules. When orders are received, the system will calculate materials, production availability and constraints. And our exclusive CONLOAD™ technology ensures that the work released to the shop floor is in full alignment with constraints, clearing any congestion and driving flow. Order statuses (and related issues) are visible throughout your organization, so your production team, supply chain management, customer service, sales and leadership are all working from the same factual, up-to-the-minute information.
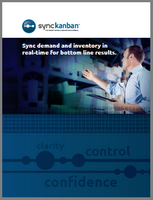
Brochure: SyncKanban® eKanban Software
eKanban Pull-Based Inventory Replenishment Software for Supply Chain Execution and Collaboration
SyncKanban® eKanban software synchronizes demand and inventory by monitoring consumption and replenishment across every facet of the manufacturing cycle in real-time. Simple to use, yet sophisticated enough to handle highly complex manufacturing environments, SyncKanban® helps right-size your inventory for bottom-line results.
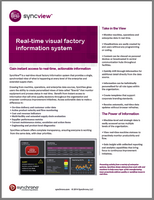
Product Information Sheet: SyncView® Software
Real-time, self-service manufacturing visualization and communication system
SyncView® is a real-time, self-service manufacturing visualization system that gives everyone the ability to monitor equipment and process status as it happens – from wherever they are. SyncView® software connects to any data source to visualize data the way you want to see it, giving you instant access to information that will drive quality decisions throughout your organization and empower continuous improvement initiatives.
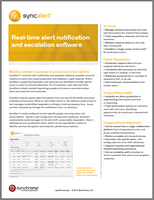
Product Information Sheet: SyncAlert® Software
Real-Time Alert Notification and Escalation Software
SyncAlert® software is a real-time alert and escalation software system that provides universal visibility to issues that impact production and mobilizes a rapid response based on your standard operating procedures.
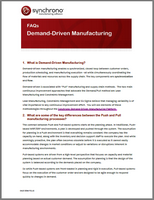
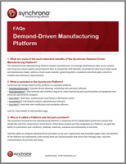
FAQs: Synchrono® Demand-Driven Manufacturing Platform
The Demand-Driven Manufacturing Platform enables the real-time factory of the future. But how? What’s included? Does it integrate with my existing systems?
Get the answers to these questions and more by downloading our FAQs.
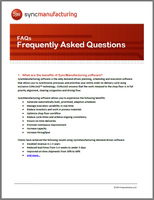
FAQs: SyncManufacturing® Software
Demand-Driven Manufacturing Planning, Scheduling and Execution
SyncManufacturing® software simplifies production scheduling, eliminating the need to build and update schedules. When orders are received, the system will calculate materials, production availability and constraints. And our exclusive CONLOAD™ technology ensures that the work released to the shop floor is in full alignment with constraints, clearing any congestion and driving flow. Order statuses (and related issues) are visible throughout your organization, so your production team, supply chain management, customer service, sales and leadership are all working from the same factual, up-to-the-minute information.
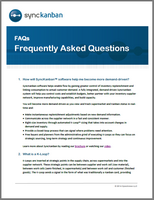
FAQs: SyncKanban® Software
eKanban Pull-Based Inventory Replenishment Software for Supply Chain Execution and Collaboration
SyncKanban® manufacturing eKanban software provides continuously refreshed, powerful information to right-size inventory levels and maximize workflow. It monitors consumption and replenishment across every facet of the manufacturing cycle – from suppliers to manufacturing to transfer kanbans – healing the performance problems that come with unsynchronized, systems. The solution also creates a collaborative relationship with suppliers and allows sales to make promises they can keep. SyncKanban® provides the ability to respond accurately and instantly from any point in the KLoop® to eliminate strains on the system before they impact delivery times or customer relationships. Data-based reporting empowers decision making and allows supply managers to focus on more value-added activities, delivering more capacity and a competitive advantage.
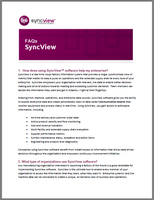
FAQs: SyncView® Software
Real-time manufacturing visualization and communication system
SyncView® is a real-time manufacturing visualization and communication system that provides a single, synchronized view of what is happening at every level of the enterprise and extended supply chain.
Drawing from machine, operations, and enterprise data sources, SyncView® gives users the ability to create personalized views of data called “Boards” that monitor equipment and process status in real time. With this level of visibility, users benefit from instant access to information that will drive quality decisions throughout the organization and empower continuous improvement initiatives with confidence and clarity.
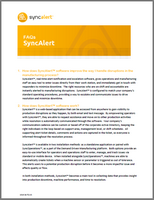
FAQs: SyncAlert® Software
Real-time alert notification and escalation software
SyncAlert® software provides universal visibility to issues that impact production and mobilizes a rapid response. Within SyncAlert®, supporting responders and resources are identified to handle specific issues in order to minimize downtime. For all machines, work cells and shifts, SyncAlert® embeds standard operating procedures to ensure consistent action plans and resolution time estimates.
Demand-Driven Matters Episode 1: What is Demand-Driven Manufacturing?
Experts define Demand-Driven Manufacturing and discuss how Demand-Driven Manufacturing enables the Industrial Internet of Things (IIoT), Factory of the Future and Industry 4.0.
Demand-Driven Matters Episode 2. The 5 Key Elements that Drive Flow – Part 1: Controlling the Release
This is the first in a series of podcast episodes that focus on The 5 Key Elements that Drive Flow for Demand-Driven Manufacturing environments. This episode focuses on the first element, Controlling the Release (Pull). Experts explain that by gating work into the system, you can maintain a constant level of flow.
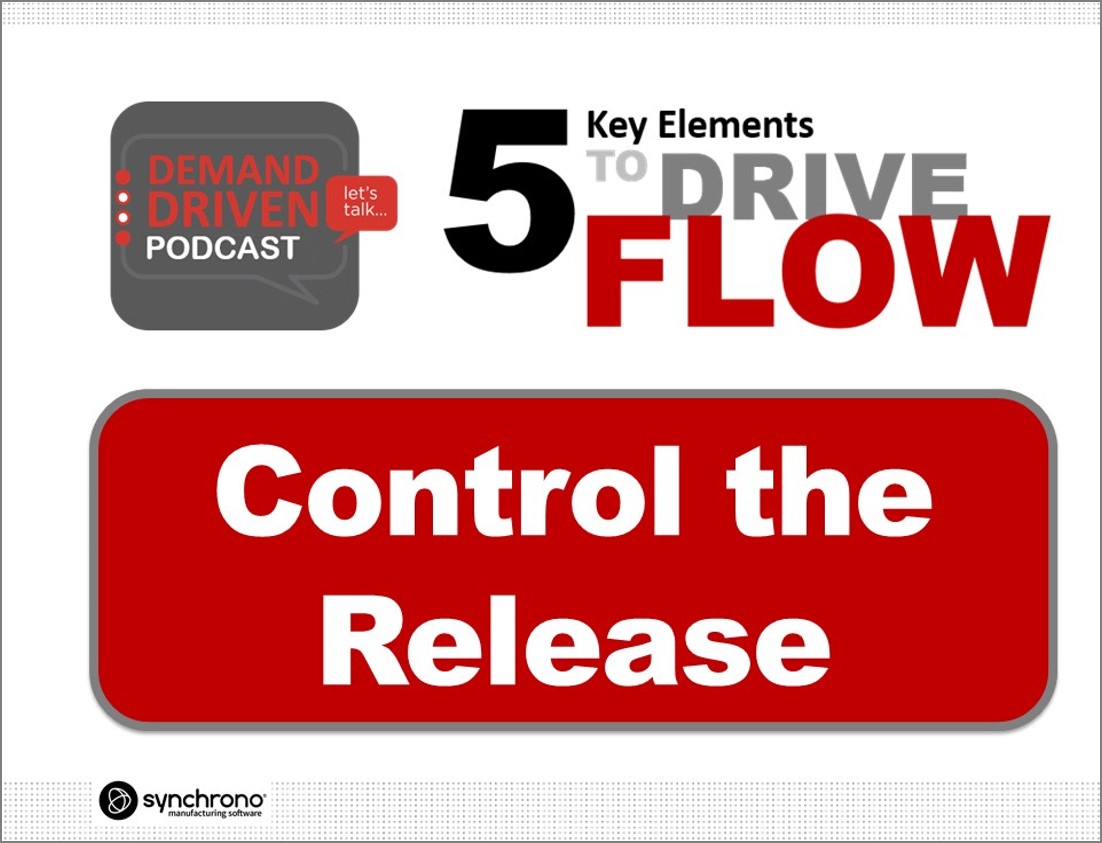
Demand-Driven Matters Episode 3. The 5 Key Elements that Drive Flow – Part 2: Synchronize Activities
This is the second in our series addressing the five key elements that drive production flow in Demand-Driven Manufacturing environments. Experts discuss the impact of synchronization – aligning people, materials, machines, method and data – and more.
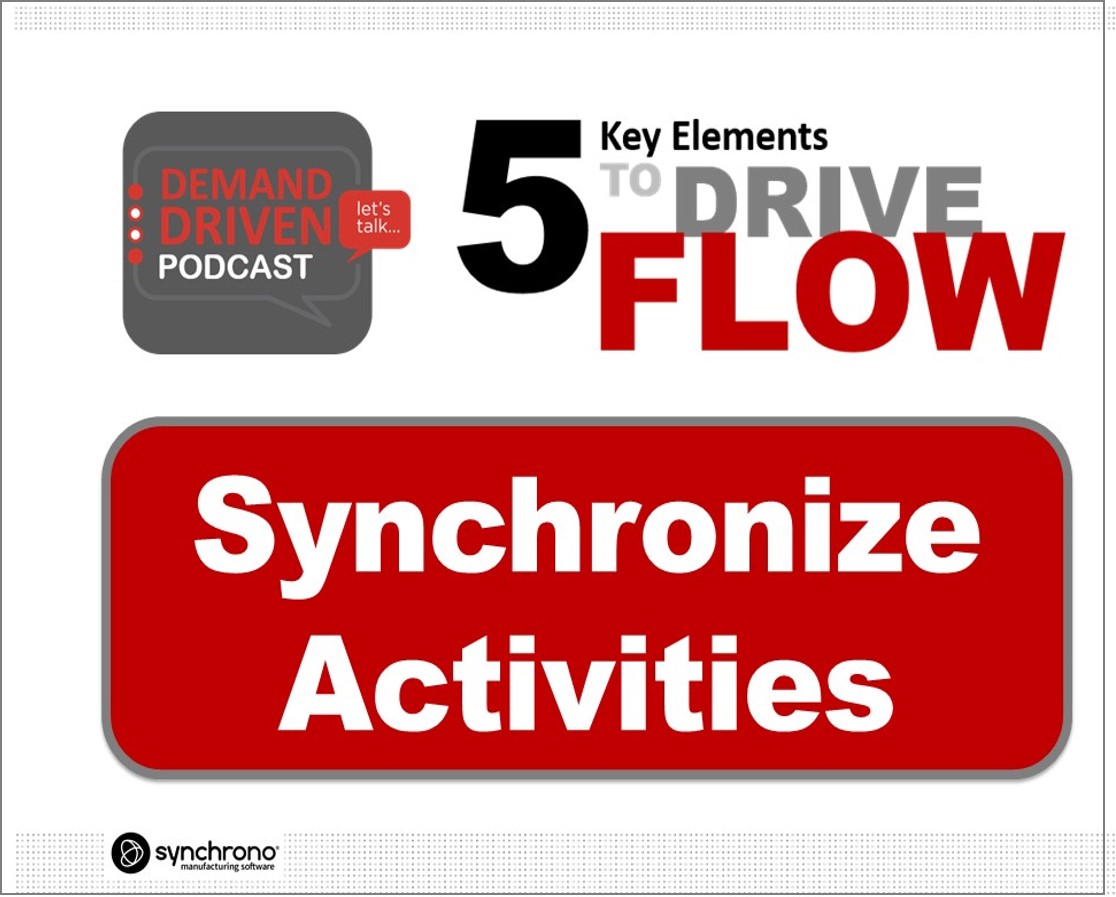
Demand-Driven Matters Episode 4. The 5 Key Elements that Drive Flow – Part 3: Continuous Improvement
Continuous Improvement is the focus in this episode; the third installment in the series, the 5 Key Elements to Drive Flow in Demand-Driven Manufacturing. Gain insight into best practices for approaching and focusing your continuous improvement efforts.
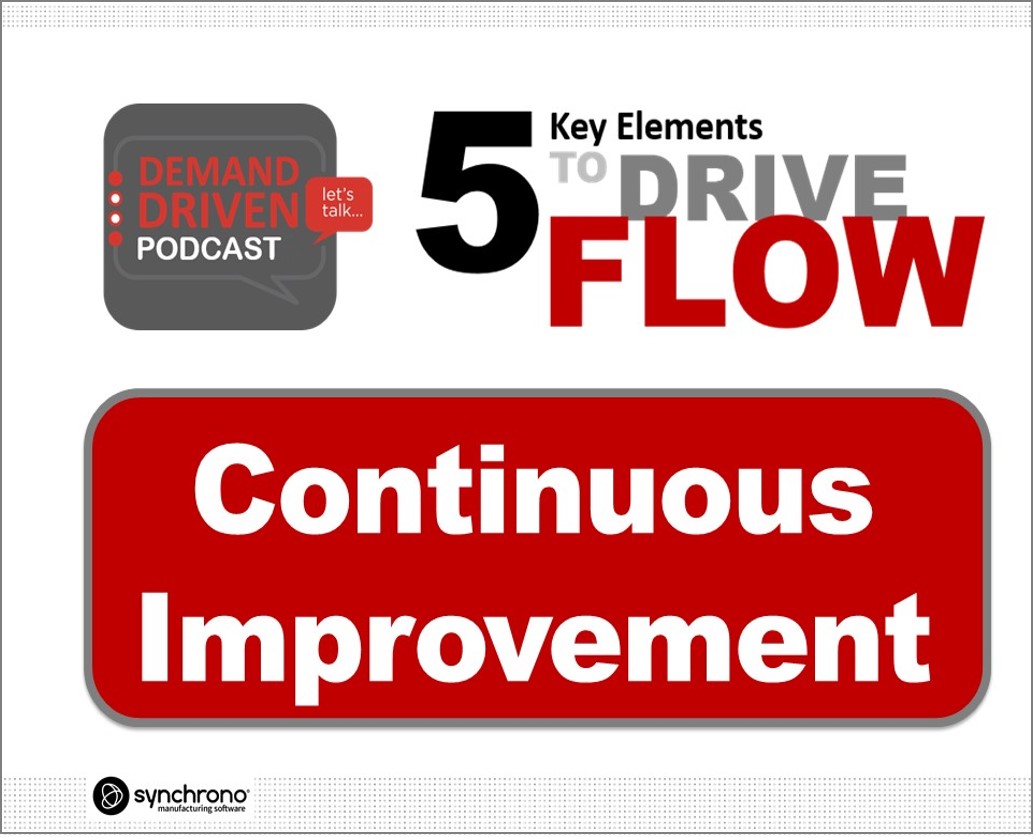
Demand-Driven Matters Episode 5. The 5 Key Elements that Drive Flow – Part 4: Extend to the Supply Chain
This episode of Demand-Driven Matters is the fourth in the series focusing on the 5 key elements that drive demand-driven manufacturing production flow. In this episode, the focus is on how to engage and synchronize the external supply chain through proactive communication, consumption-based replenishment and more.
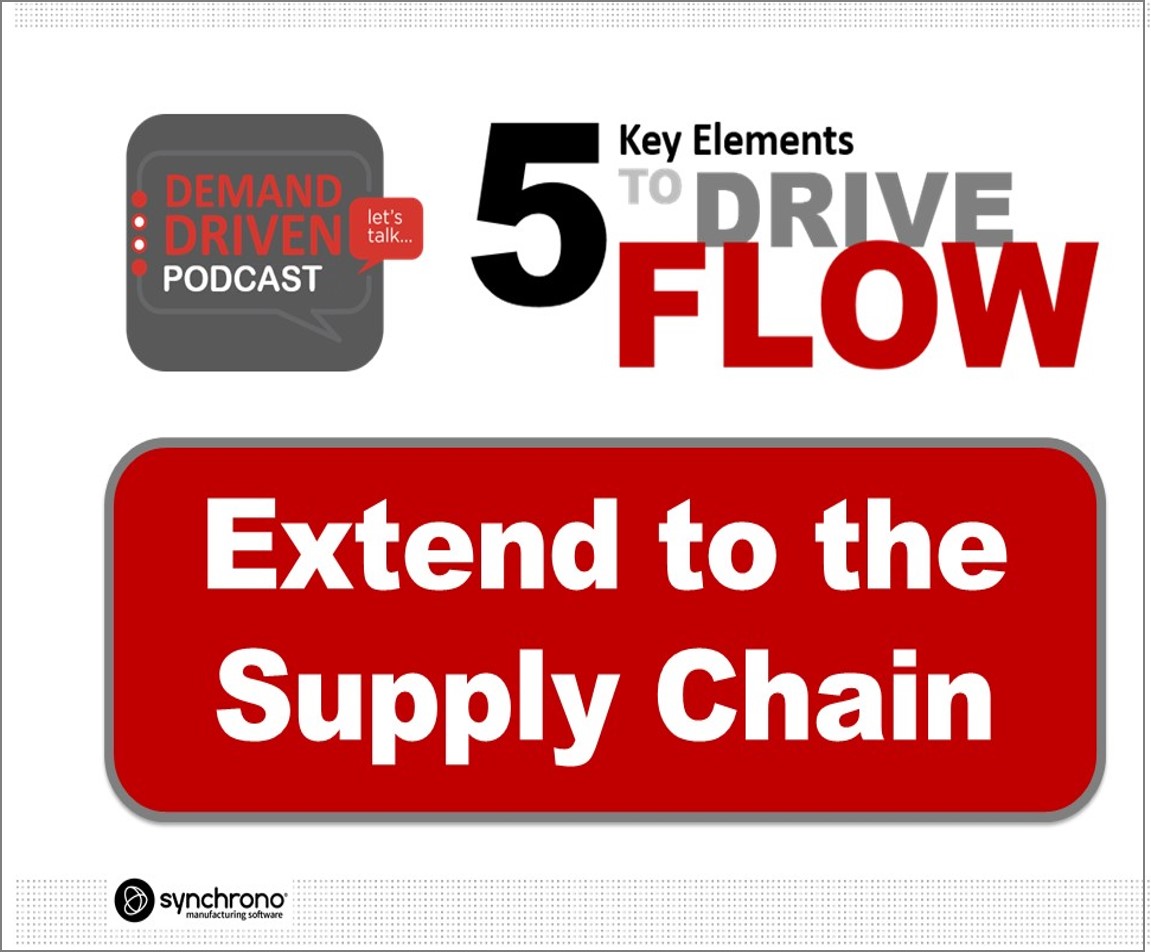
Demand-Driven Matters Episode: The 5 Key Elements that Drive Flow – Part 5: Align Metrics
This, the final installment in the series, 5 Key Elements to Drive Flow, focuses on metrics. Experts discuss suggested metrics to focus on to improve and maintain an optimal rate of production flow.